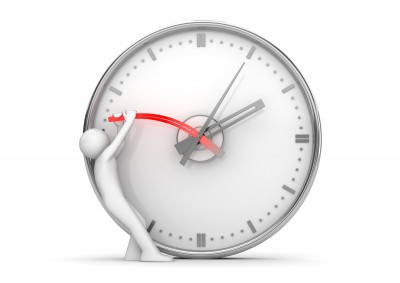
The majority of journals publish articles about supply chain management. The number and type of articles published will depend on the journal. Most articles are focused upon SMEs or high-demand items. Some articles discuss the agency theory and its impact on supply chain management. The next section provides an overview of the articles published in various journals.
Trends in articles on supply chain management
Most businesses rely on their supply chains to survive. They need to function seamlessly, no matter whether it's online or offline, in order to satisfy customer expectations. Supply chain disruptions can affect every aspect of a business's operations. However, supply chain trends and statistics can help prepare businesses for any changes that may arise.

There are many factors that influence supply chain evolution, such as customer expectations and technological innovations. Companies need to be able handle multiple customer channels, fulfillment models, payment options, physical systems, and other factors. Artificial intelligence (AI), is being used by some companies to improve their supply chains. This technology is expected not only to save money but it will also accelerate processes.
Association of affiliated researchers in articles on supply chain management
The Association of Affiliated Researchers in Articles on Supply Chain Management publishes a ranking of supply management research output. This is based on the number of publications in five years. Submissions are assessed for their relevance to the program theme, the rigor and the meaningful advancement of supply chain management knowledge.
AAF publishes reports based on a wide range of topics, including the role of supply chain professionals in the global economy. These research findings offer insight into trends in supply chain management and procurement. These topics include planning for supply chain, forecasting, big-data, inventory management, sales and operations planning, as well as forecasting.
The majority of articles concern SMEs.
Although the majority of articles on supply-chain management focus on large, global organizations, others focus on small and medium enterprises (SMEs). Zowada (2011) argues, "The key to linkage" is the ability of SMEs be flexible and adaptable. These factors are critical in creating a competitive disadvantage.
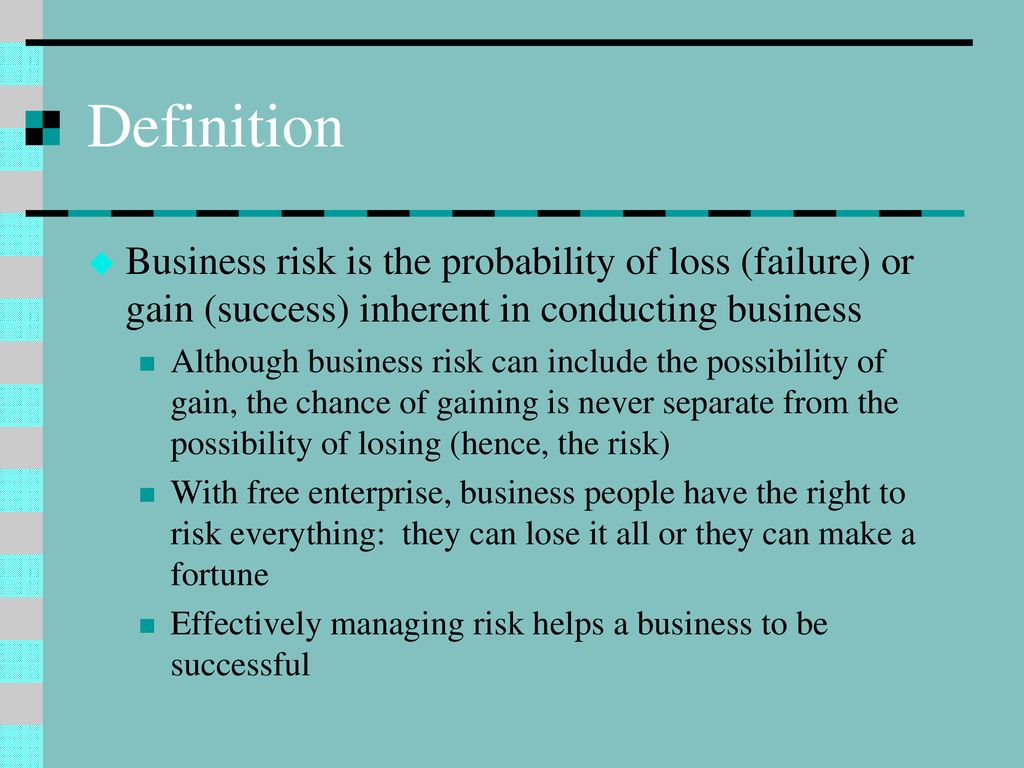
SME contribute enormously to GDP, employment, exports, GDP and other economic activities. However, they are increasingly facing threats that could stifle their growth. Fortunately, governments can use their past success to develop programs to help SMEs prosper in today's global economy.
FAQ
What kind of people use Six Sigma
Six-sigma will be well-known to anyone who has worked in operations research or statistics. Anybody involved in any aspect or business can benefit.
This requires a lot of dedication, so only people with great leadership skills can make the effort to implement it.
What is TQM and how can it help you?
The industrial revolution saw the realization that prices alone were not sufficient to sustain manufacturing companies. This led to the birth of quality. They needed to improve the quality and efficiency of their products if they were to be competitive.
Management realized the need to improve and created Total Quality Management, which focused on improving all aspects within an organization's performance. It included continual improvement processes, employee involvement, customer satisfaction, and customer satisfaction.
What is the difference in Six Sigma and TQM?
The main difference between these two quality-management tools is that six-sigma concentrates on eliminating defects while total QM (TQM), focuses upon improving processes and reducing expenses.
Six Sigma is a method for continuous improvement. It emphasizes the elimination or minimization of defects through statistical methods such control charts and p charts.
The goal of this method is to reduce variation in product output. This is done by identifying root causes and rectifying them.
Total Quality Management involves monitoring and measuring every aspect of the organization. It also involves training employees to improve performance.
It is frequently used as an approach to increasing productivity.
What can a manager do to improve his/her management skillset?
You can improve your management skills by practicing them at all times.
Managers must monitor the performance of subordinates constantly.
You must quickly take action if your subordinate fails to perform.
You must be able to spot what is lacking and how you can improve it.
Why is it important that companies use project management methods?
Project management techniques can be used to ensure smooth project execution and meeting deadlines.
This is because most businesses rely on project work for their products and services.
Companies must manage these projects effectively and efficiently.
Companies could lose their time, reputation, and money without effective project management.
What is the role of a manager in a company?
The role of a manager varies from one industry to another.
In general, a manager controls the day-to-day operations of a company.
He/she will ensure that the company fulfills its financial obligations.
He/she is responsible for ensuring that employees comply with all regulations and follow quality standards.
He/she plans and oversees marketing campaigns.
Statistics
- This field is expected to grow about 7% by 2028, a bit faster than the national average for job growth. (wgu.edu)
- Hire the top business lawyers and save up to 60% on legal fees (upcounsel.com)
- 100% of the courses are offered online, and no campus visits are required — a big time-saver for you. (online.uc.edu)
- As of 2020, personal bankers or tellers make an average of $32,620 per year, according to the BLS. (wgu.edu)
- The profession is expected to grow 7% by 2028, a bit faster than the national average. (wgu.edu)
External Links
How To
How can you create a Quality Management Plan, (QMP)?
QMP (Quality Management Plan) is a system to improve products and services by implementing continuous improvement. It is about how to continually measure, analyze, control, improve, and maintain customer satisfaction.
QMP stands for Quality Management Process. It is used to guarantee good business performance. QMP helps improve production, service delivery and customer relationships. QMPs should address all three dimensions: Products, Services, and processes. When the QMP includes only one aspect, it is called a "Process" QMP. QMP stands for Product/Service. QMP stands for Customer Relationships.
When implementing a QMP, there are two main elements: Scope and Strategy. These elements are as follows:
Scope: This is the scope of the QMP and its duration. For example, if your organization wants to implement a QMP for six months, this scope will define the activities performed during the first six months.
Strategy: This describes the steps taken towards achieving the goals set forth in the scope.
A typical QMP comprises five phases: Planning and Design, Development, Construction, Implementation, Maintenance. Below is a description of each phase:
Planning: This stage identifies and prioritizes the QMP's objectives. All stakeholders involved in the project are consulted to understand their requirements and expectations. After identifying the objectives, priorities, and stakeholder involvement, the next step is to develop the strategy for achieving these objectives.
Design: During this stage, the design team develops the vision, mission, strategies, and tactics required for the successful implementation of the QMP. These strategies are put into action by developing detailed plans and procedures.
Development: Here the development team works toward building the necessary resources and capabilities to support the successful implementation.
Implementation is the actual implementation of QMP according to the plans.
Maintenance: It is an ongoing process that maintains the QMP over time.
The QMP must also include several other items:
Participation by Stakeholders is essential for the QMP's continued success. They need to be actively involved in the planning, design, development, implementation, and maintenance stages of the QMP.
Project Initiation: It is essential to have a clear understanding about the problem and the solution before you can initiate a project. The initiator must know the reason they are doing something and the expected outcome.
Time Frame: The time frame of the QMP is very critical. For a short time, you can start with the simple version of the QMP. If you're looking to implement the QMP over a longer period of time, you may need more detailed versions.
Cost Estimation is another important aspect of the QMP. Without knowing how much you will spend, planning is impossible. The QMP should be cost-estimated before it can begin.
QMPs are more than just documents. They can also be updated as needed. It changes with the company. So, it should be reviewed periodically to make sure that it still meets the needs of the organization.