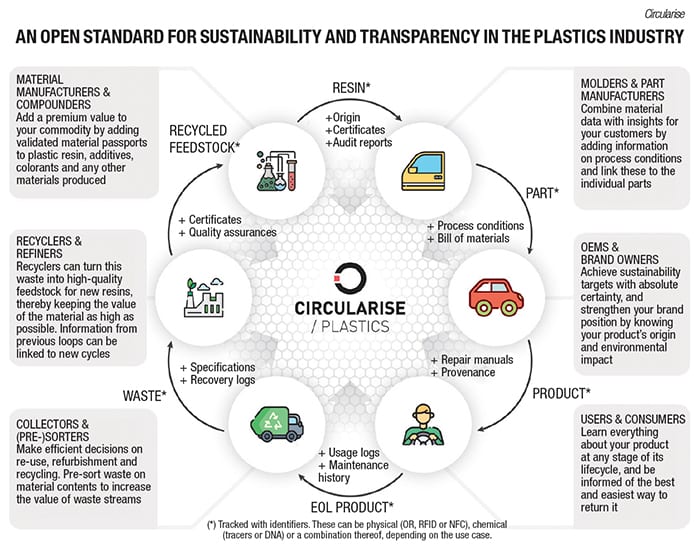
Process safety management aims to ensure that operating systems and processes are safe. This system is a legal requirement for major hazard facilities and must be updated at least every five years. Process safety management is designed to prevent accidents. These steps will help you get started with process management. These steps will make your facility as safe as possible, and prevent accidents.
Process safety management can be described as a disciplined framework that manages the integrity of operating system and process processes.
Process safety management's goal is to decrease the number of incidents. This will increase sustained value and productivity. It emphasizes the control of risks within the plant, and inherently safer machinery. It requires strict adherence and assessment of hazards. It includes training, maintenance, and control of process. It is an essential element of a safety-conscious business.
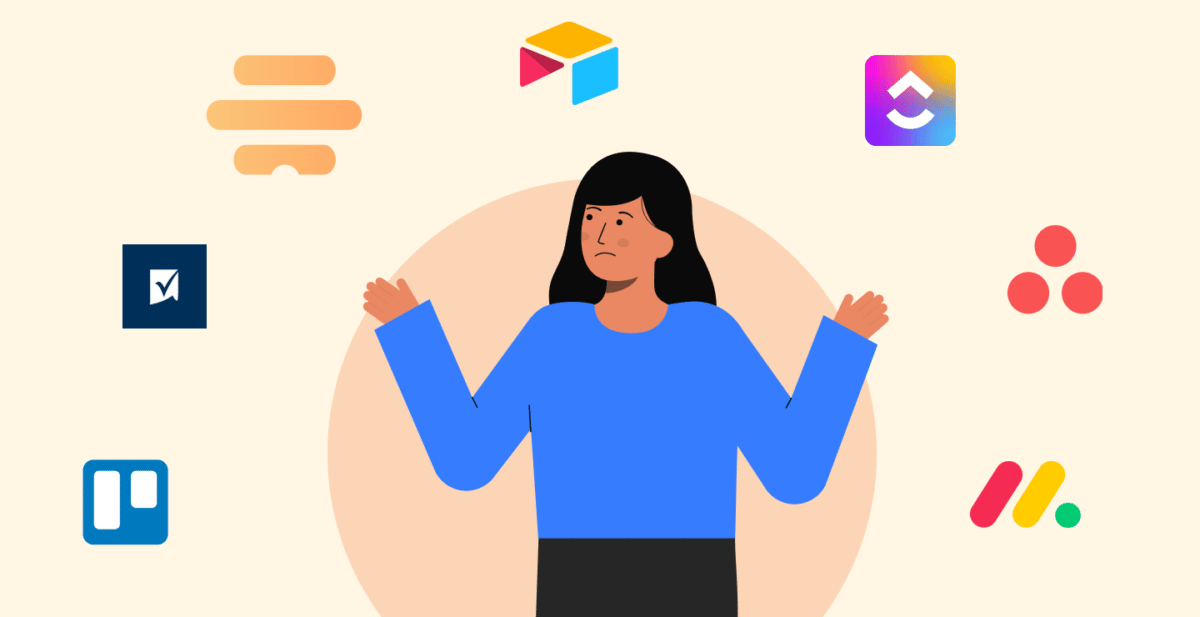
It must be kept current every 5 year
OSHA's Occupational Safety and Health Administration (OSHA), requires that processes are regularly reviewed and revised. This includes the development and updating of safety procedures and processes. All employees must have access to this information. Written procedures and investigation reports must be kept for five years. Updated process safety information must be readily available for employees to review and follow. Employers can seek the assistance of safety risk management consultants to meet their requirements.
It is a legal requirement to have major hazard equipment.
For all major hazard areas, the process safety management system must be implemented. In addition to developing and implementing the program, employers must implement a procedure for a prompt and safe evacuation of employees. In most cases, this plan includes a safety alarm that will alert employees to evacuate. The plan should include emergency procedures for employees who are unable to evacuate from the hazardous area.
It helps prevent incidents
A well-designed process safety system can help improve profitability, safety performance, as well as quality. It can also help improve the company’s environmental responsibility. It can also help reduce incidents. These are four key areas for long-term success in a company. Below is a short overview of the numerous benefits of a safety management system. In short, it helps a company prevent accidents and improve the health and safety of its employees and customers.
It is time-consuming.
It can be difficult and time-consuming to implement process safety management in hazardous chemical facilities. OSHA doesn't regulate the implementation of process safety management systems, but it does require facilities with at least 14 requirements to submit a written plan. For data collection and compilation of risk assessments, and other information, spreadsheets and forms are used by some companies. This takes time and can lead to human error.
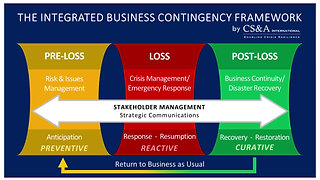
Participation by employees is necessary
Pennsylvania State University has adopted a PSM program with an Employee Participation component. This element draws on employees' experience and knowledge to increase safety. The program describes different mechanisms for employee participation and identifies minimum requirements for participation. All employees should be included in the safety management process. To avoid serious incidents, employee participation in PSM can be crucial. How do you ensure employees are fully engaged in the PSM program?
FAQ
How does a manager motivate their employees?
Motivation refers to the desire to perform well.
It is possible to be motivated by doing something you enjoy.
Or you can get motivated by seeing yourself making a contribution to the success of the organization.
If you are a doctor and want to be one, it will likely be more rewarding to see patients than to read medical books every day.
Motivation comes from within.
You may feel strongly that you are responsible to help others.
Perhaps you enjoy working hard.
If you don't feel motivated, ask yourself why.
Then think about how you can make your life more motivating.
What is Kaizen, exactly?
Kaizen is a Japanese term meaning "continuous improvement." It is a philosophy that encourages employees to constantly look for ways to improve their work environment.
Kaizen is based upon the belief that each person should be capable of doing his or her job well.
Six Sigma is so popular.
Six Sigma is easy to use and can lead to significant improvements. It also provides a framework for measuring improvements and helps companies focus on what matters most.
What are some common management mistakes?
Sometimes, managers make their job more difficult than it is.
They might not give enough support and delegate the right responsibilities to their staff.
Managers often lack the communication skills necessary to motivate and guide their teams.
Some managers create unrealistic expectations for their teams.
Some managers may try to solve every problem themselves instead of delegating responsibility to others.
Statistics
- Your choice in Step 5 may very likely be the same or similar to the alternative you placed at the top of your list at the end of Step 4. (umassd.edu)
- The profession is expected to grow 7% by 2028, a bit faster than the national average. (wgu.edu)
- Our program is 100% engineered for your success. (online.uc.edu)
- This field is expected to grow about 7% by 2028, a bit faster than the national average for job growth. (wgu.edu)
- Hire the top business lawyers and save up to 60% on legal fees (upcounsel.com)
External Links
How To
How do you get your Six Sigma license?
Six Sigma is a quality control tool that improves processes and increases efficiency. Six Sigma is a method that helps companies get consistent results from their operations. The name "Sigmas" comes from the Greek words "sigmas", meaning "six". Motorola was the first to develop this process. Motorola recognized that they had to standardize their manufacturing processes to produce faster and more affordable products. Due to the different workers involved, there was a lack of consistency. To resolve this issue, they used statistical tools like Pareto analysis and control charts. They would then apply these techniques to all aspects of their operation. This technique would enable them to make improvements in areas that needed it. There are three main steps to follow when trying to get your Six Sigma certification. Find out if you are qualified. Before you can take any tests, you will need to take some classes. After you have passed the classes, you can start taking the exams. You'll need to go back and review all the information you received in class. Next, you'll be ready for the test. If you pass, you'll get certified. Finally, you can add your certifications on to your resume.