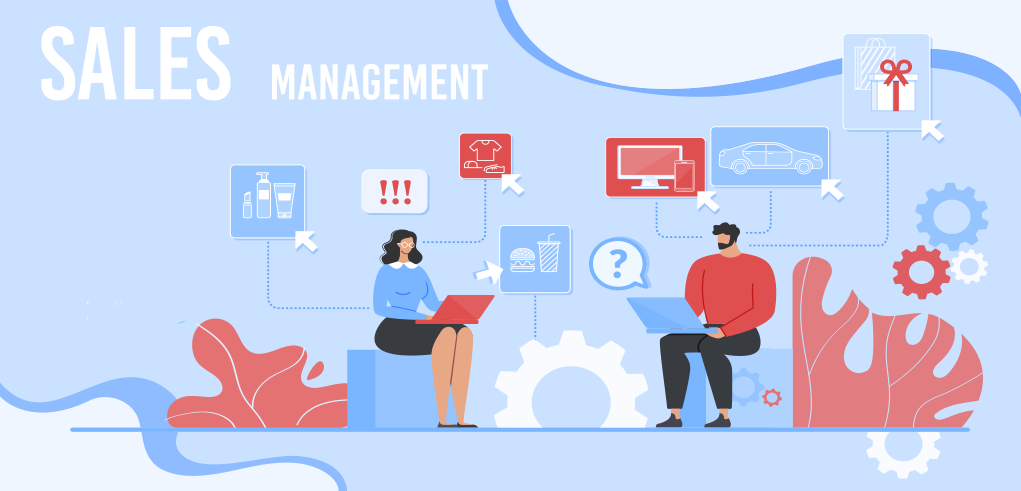
In the past, interest rate risk has been a constant in the banking industry. This risk arises from mismatches between bank's assets maturity and its liabilities on its balance sheets. The projected earnings of banks can be affected if there is a difference in the cash flows expected by assets and liabilities. To help manage interest rate risk, financial institutions may use two methods.
One way is to calculate the impact of changes in interest rate over a 12- to 24 month period. This method is called an income simulation. The income simulation results are then compared against a base case scenario.
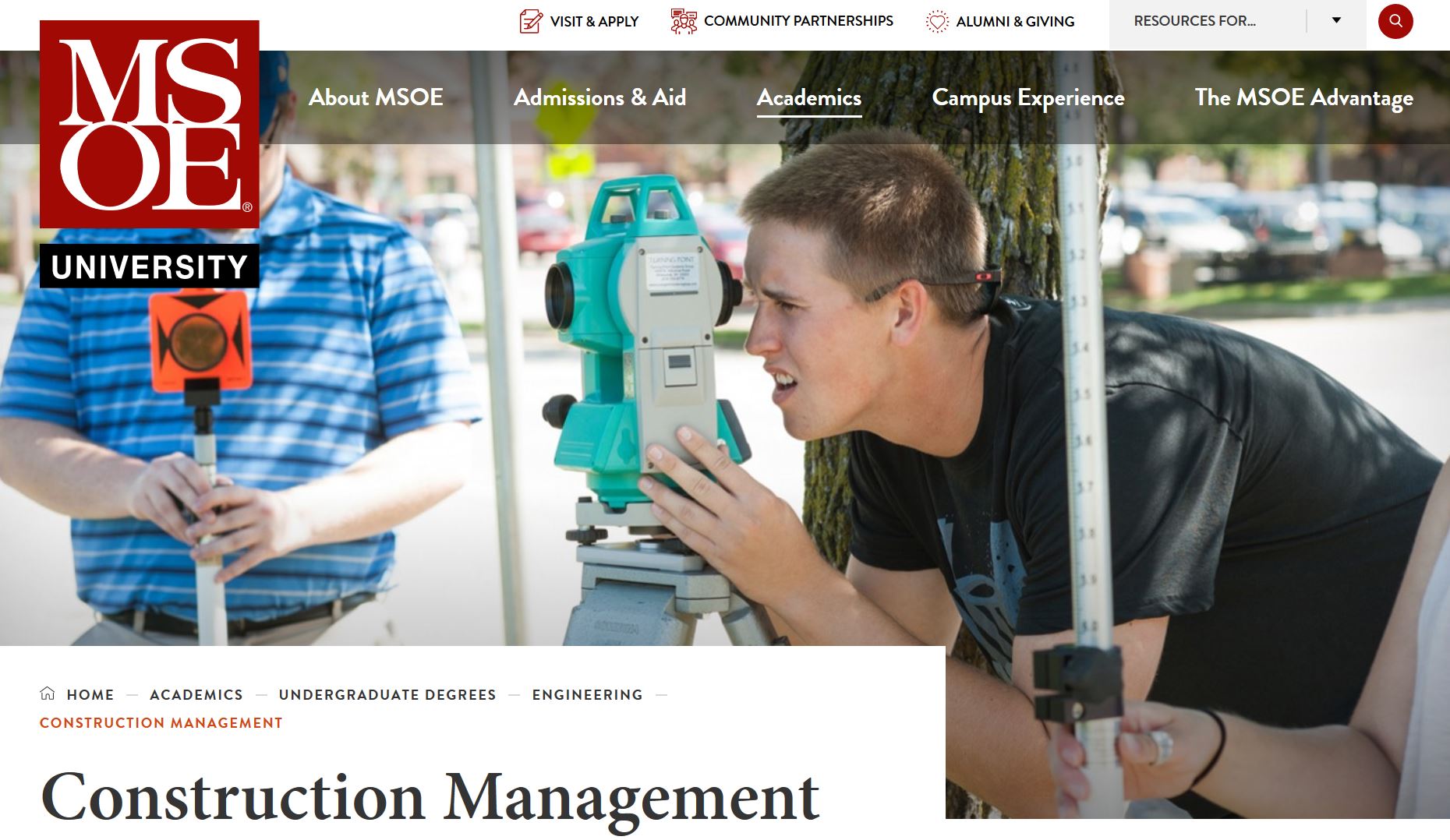
Another method, the economic value and equity (EVE), is a more long-term economic measure. It's used for evaluating a bank’s interest rate risk and to calculate the potential capital changes in response. EVE is calculated by taking into account interest rate movements and adjusting the capital to ensure liquidity. EVE can also be used to measure structural risk. This is risk that results from bank balance sheet mismatches.
Market price sensitivity is another indicator of interest rate risk. Market rates are used to protect financial instruments. They can impact cash flows and their value. Financial institutions have to manage their risk and accept risks in order to earn returns. This risk may also affect the underlying value of an institution's balance sheet. If an institution has to take risk to generate returns, it must also manage its risks wisely. It can do so by performing stress tests, which are used to evaluate the bank's need for additional capital, as well as to determine the bank's balance sheet management strategies. Stress tests are usually used to assess the effect of fluctuations in interest rates on an institution’s budget. The results of stress tests are used to assess the risk appetite of an institution and determine whether or not to invest in new assets. Stress tests are used to assess limit work and are monitored and reported regularly.
An escrow model is a third way to measure adverse effects that result from changes in interest rates. The quantity of an escrow is the amount that equity market values decline due to changes in rates. Escrow models are less commonly used to measure value at risk.
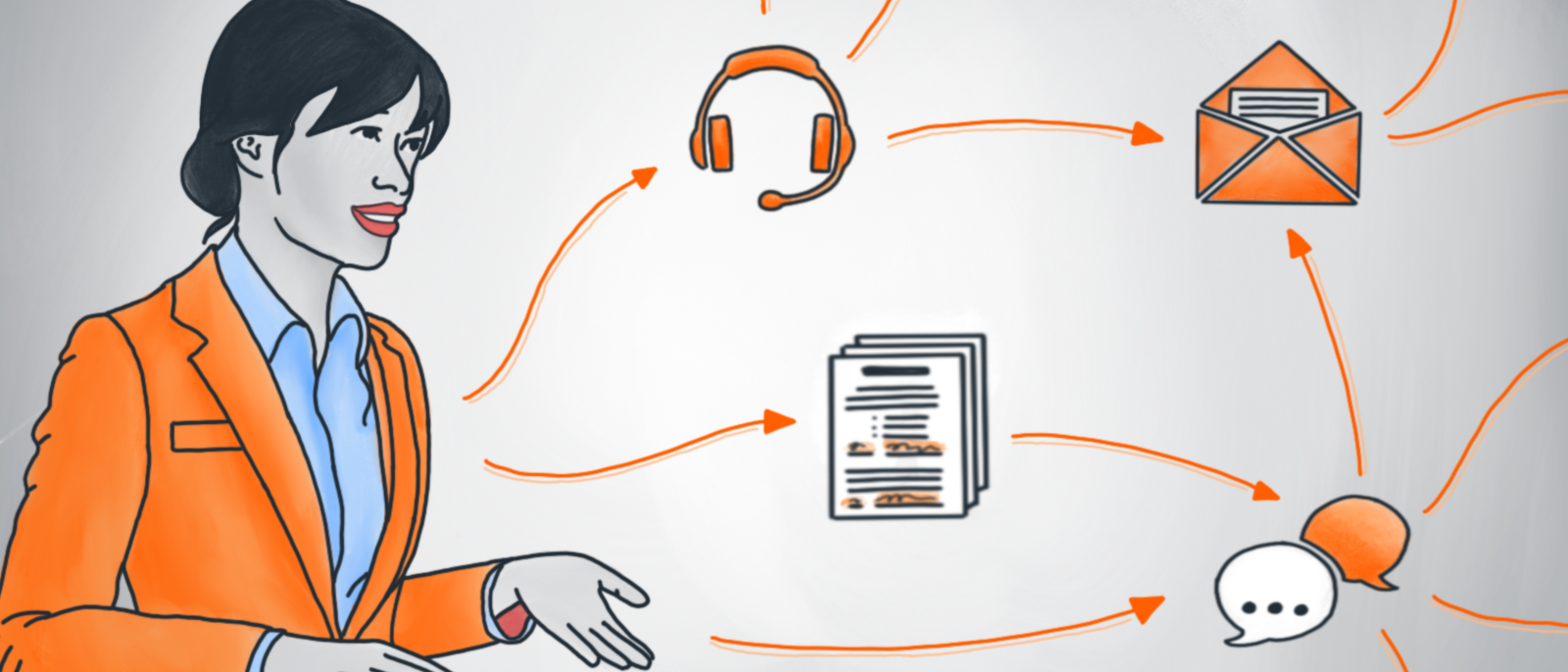
A majority of community banks do an income simulation in order to calculate their exposure to interest rates over a 12-month- or 24-month time span. This is the most common method used to calculate earnings at risk. The results are compared with a base case scenario and income and expenses are recalculated for higher or lower interest rates. The bank's earnings subject to risk is then compared against its peers to determine its performance.
FAQ
What are the steps that management takes to reach a decision?
The decision-making process for managers is complex and multifaceted. It involves many factors, such as analysis and strategy, planning, execution, measurement, evaluation, feedback etc.
The key thing to remember when managing people is that they are human beings just as you are and therefore make mistakes. As such, there are always opportunities for improvement, especially when you put in the effort to improve yourself.
This video shows you how management makes decisions. We discuss different types of decisions as well as why they are important and how managers can navigate them. You'll learn about the following topics:
What is Six Sigma?
It's a method for quality improvement that focuses on customer service as well as continuous learning. The goal is to eliminate defects by using statistical techniques.
Six Sigma was developed at Motorola in 1986 as part of its efforts to improve manufacturing processes.
The idea quickly spread in the industry. Many organizations today use six-sigma methods to improve product design and production, delivery and customer service.
How can a manager improve his/her managerial skills?
Good management skills are essential for success.
Managers must monitor the performance of subordinates constantly.
If you notice your subordinate isn't performing up to par, you must take action quickly.
You should be able pinpoint what needs to improve and how to fix it.
What is the difference of a program and project?
A program is permanent, whereas a project is temporary.
Projects usually have a goal and a deadline.
It is often done in a team that reports to another.
A program usually has a set of goals and objectives.
It is often done by one person.
What role can a manager fill in a company’s management?
Each industry has a different role for a manager.
The manager oversees the day-to-day activities of a company.
He/she ensures that the company meets its financial obligations and produces goods or services that customers want.
He/she ensures employees adhere to all regulations and quality standards.
He/she plans new products and services and oversees marketing campaigns.
What's the difference between Six Sigma and TQM?
The major difference between the two tools for quality management is that six Sigma focuses on eliminating defect while total quality control (TQM), on improving processes and decreasing costs.
Six Sigma stands for continuous improvement. It emphasizes the elimination and improvement of defects using statistical methods, such as control charts, P-charts and Pareto analysis.
The goal of this method is to reduce variation in product output. This is accomplished through identifying and correcting root causes.
Total quality management involves measuring and monitoring all aspects of the organization. Training employees is also part of total quality management.
It is often used as a strategy to increase productivity.
What's the difference between leadership & management?
Leadership is about being a leader. Management is about controlling others.
Leaders inspire others, managers direct them.
A leader motivates people to achieve success; a manager keeps workers on task.
A leader develops people; a manager manages people.
Statistics
- Our program is 100% engineered for your success. (online.uc.edu)
- UpCounsel accepts only the top 5 percent of lawyers on its site. (upcounsel.com)
- Your choice in Step 5 may very likely be the same or similar to the alternative you placed at the top of your list at the end of Step 4. (umassd.edu)
- This field is expected to grow about 7% by 2028, a bit faster than the national average for job growth. (wgu.edu)
- The profession is expected to grow 7% by 2028, a bit faster than the national average. (wgu.edu)
External Links
How To
How does Lean Manufacturing work?
Lean Manufacturing is a method to reduce waste and increase efficiency using structured methods. They were created in Japan by Toyota Motor Corporation during the 1980s. The primary goal was to make products with lower costs and maintain high quality. Lean manufacturing focuses on eliminating unnecessary steps and activities from the production process. It is made up of five elements: continuous improvement, continuous improvement, just in-time, continuous change, and 5S. Pull systems involve producing only what the customer wants without any extra work. Continuous improvement involves constantly improving upon existing processes. Just-in-time refers to when components and materials are delivered directly to the point where they are needed. Kaizen refers to continuous improvement. It is achieved through small changes that are made continuously. The 5S acronym stands for sort in order, shine standardize and maintain. To achieve the best results, these five elements must be used together.
Lean Production System
Six key concepts form the foundation of the lean production system:
-
Flow - The focus is on moving information and material as close as possible to customers.
-
Value stream mapping: This is a way to break down each stage into separate tasks and create a flowchart for the entire process.
-
Five S's - Sort, Set In Order, Shine, Standardize, and Sustain;
-
Kanban – visual signals like colored tape, stickers or other visual cues are used to keep track inventory.
-
Theory of constraints: identify bottlenecks in your process and eliminate them using lean tools, such as kanban board.
-
Just-in time - Get components and materials delivered right at the point of usage;
-
Continuous improvement is making incremental improvements to your process, rather than trying to overhaul it all at once.