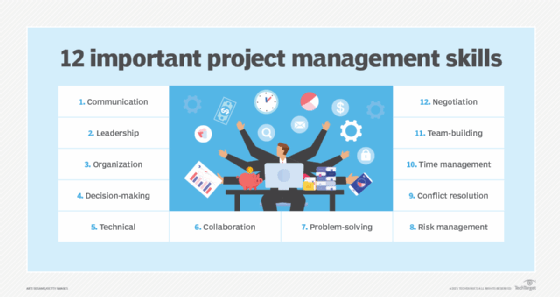
The supply chain webinars are a great way learn about current trends and how they can impact your business. Many of them are free and open to everyone. Learn more about Supply Chain Management, AI and Machine Learning. Many of these events also touch upon Industry 4.0 technologies as well as Multiparty control towers. These events are great opportunities to get the latest information on supply chain technology, whether you are a business leader or looking for new ideas for your company.
Machine Learning
Machine Learning can be applied to your supply chain in many different ways. It can help optimize factory schedules, balance make-to-order/made-to-stock workflows, prevent material delays in production, and more. Machine learning can also be used to detect fraud. It analyzes real-time data and looks for anomalies and pattern deviations, notifying supply chain managers of possible problems.
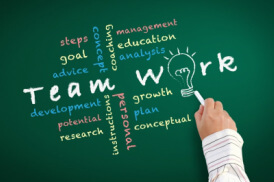
AI
Predictive analysis is an excellent tool for supply chains. It can be difficult to interpret the data generated by this technology. This webinar will help supply chains managers understand the basics behind AI and how it can be applied in their business.
Industry 4.0 technologies
Industry 4.0 technologies, otherwise known as the digital supply chain, are a major shift in the way businesses conduct business. The speed of change makes it challenging to distill the competitive advantage from the new technologies. This Capstone Webinar will cover the key domains, change agents, and drivers of transformation. This webinar will address many of the most frequently asked questions regarding key technologies.
Multiparty control towers
Multiparty control Towers are an essential part of the supply-chain ecosystem. They are a great way for companies to automate repetitive tasks while saving time and money. When combined with orchestration platforms, multiparty command towers can be powerful tools. These solutions connect all the parts of a supply chains ecosystem and provide one source of truth to all parties.
Collaboration throughout the supply chains
Collaboration in the supply chain is a growing trend that can bring significant benefits to a company’s bottom line. Collaboration can not only improve operational efficiency but also foster innovation and better risk management. Although collaboration can be achieved in vertical and horizontal dimensions there are some key points to keep in mind.
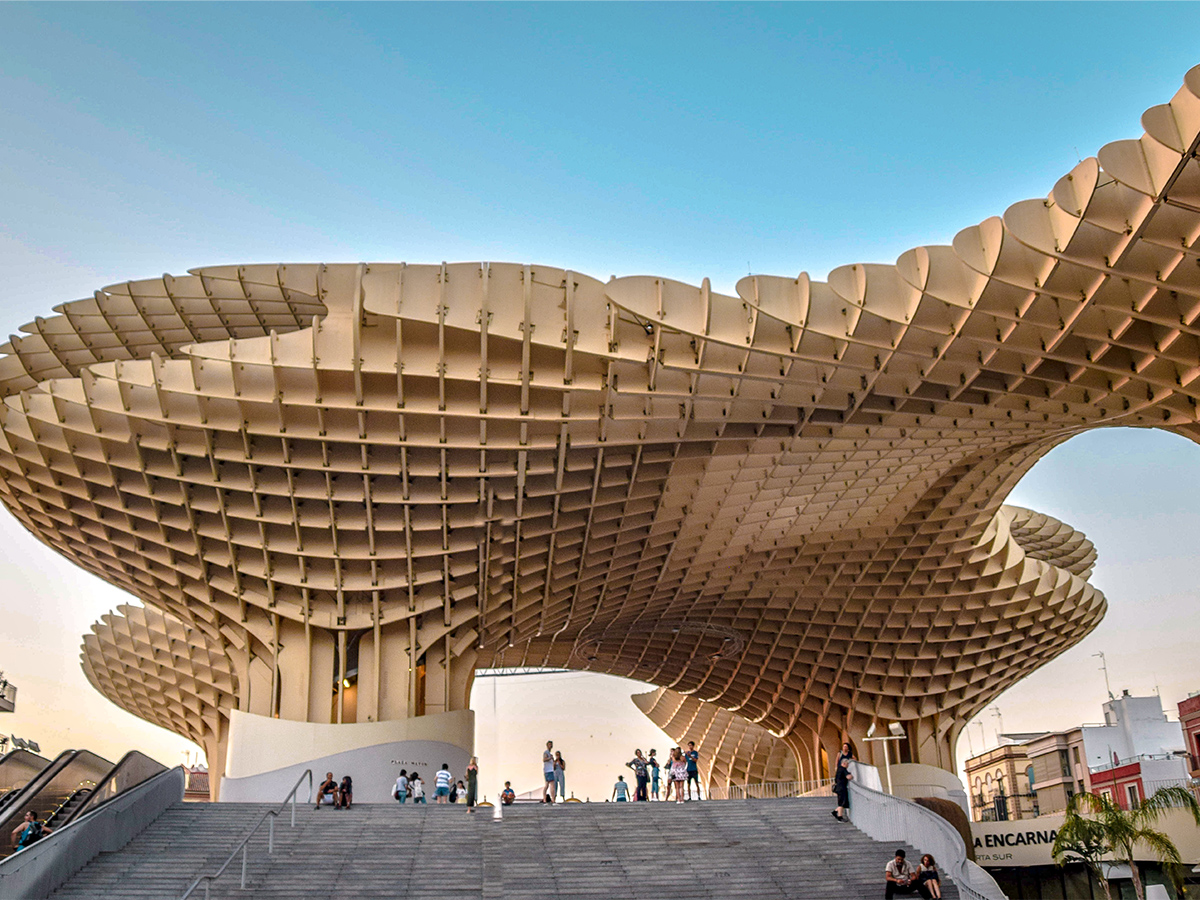
The future of the supply chain
The webinars on the Future of the Supply Chain address issues that affect supply chains. They will discuss how to make them more sustainable, integrate corporate governance in value chains, and improve access for consumers to medicines and medical devices. The speakers will also discuss how they can deal with increasing antitrust and ESG issues. The session will address trends in supply chains beginning in 2022 and beyond.
FAQ
What is the difference between project and program?
A program is permanent while a project can be temporary.
A project has usually a specified goal and a time limit.
It is often done in a team that reports to another.
A program will usually have a set number of goals and objectives.
It is often done by one person.
How does a manager motivate their employees?
Motivation refers to the desire to perform well.
Engaging in something fun can be a great way to get motivated.
Another way to get motivated is to see yourself as a contributor to the success of the company.
For example: If you want to be a doctor, you might find it more motivating seeing patients than reading medical books all day.
A different type of motivation comes directly from the inside.
You may feel strongly that you are responsible to help others.
Or you might enjoy working hard.
If you don’t feel motivated, find out why.
Then, consider ways you could improve your motivation.
How do we create a company culture that is productive?
A successful company culture is one that makes people feel valued and respected.
It is based on three principles:
-
Everyone has something to contribute
-
People are treated fairly
-
Individuals and groups can have mutual respect
These values can be seen in the behavior of people. They will show consideration and courtesy to others.
They will listen to other people's opinions respectfully.
And they will encourage others to share ideas and feelings.
Company culture also encourages open communication, collaboration, and cooperation.
People can freely express their opinions without fear or reprisal.
They understand that mistakes can be forgiven as long as they're dealt with honestly.
Finally, the company culture promotes integrity and honesty.
Everyone knows that they must always tell truth.
Everyone knows that there are rules and regulations that apply to them.
Nobody expects to be treated differently or given favors.
How do you manage your employees effectively?
Achieving employee happiness and productivity is key to managing them effectively.
This also involves setting clear expectations and monitoring their performance.
Managers must be clear about their goals and those of their teams in order to succeed.
They need to communicate clearly and openly with staff members. They also need to make sure that they discipline and reward the best performers.
They also need to keep records of their team's activities. These include:
-
What did we accomplish?
-
How much work was done?
-
Who did it?
-
It was done!
-
Why was this done?
This information can be used to monitor performance and evaluate results.
What are the 4 major functions of management
Management is responsible for organizing, managing, directing and controlling people, resources, and other activities. It includes the development of policies and procedures as well as setting goals.
Management assists an organization in achieving its goals by providing direction, coordination and control, leadership, motivation, supervision and training, as well as evaluation.
The following are the four core functions of management
Planning - Planning is about determining what must be done.
Organizing: Organizing refers to deciding how things should work.
Direction - This is the art of getting people to follow your instructions.
Controlling – Controlling is the process of ensuring that tasks are completed according to plan.
What are the five management processes?
These five stages are: planning, execution monitoring, review and evaluation.
Planning means setting goals for the long-term. This includes setting goals for the future and defining what you want.
Execution happens when you actually do the plan. They must be followed by all parties.
Monitoring is the act of monitoring your progress towards achieving your targets. Regular reviews of performance against targets, budgets, and other goals should be part.
Every year, there are reviews. These reviews allow you to evaluate whether the year was successful. If not, it is possible to make improvements for next year.
After each year's review, evaluation occurs. It helps to determine what worked and what didn’t. It also gives feedback on how well people did.
What are the main styles of management?
There are three types of management: participative, laissez faire, and authoritarian. Each style has strengths and flaws. Which style do YOU prefer? Why?
Autoritarian - The leader sets direction and expects everyone else to follow it. This style is best when the organization has a large and stable workforce.
Laissez-faire: The leader lets each person decide for themselves. This approach works best in small, dynamic organizations.
Participative: The leader listens to everyone's ideas and suggestions. This style is most effective in smaller organizations, where everyone feels valued.
Statistics
- As of 2020, personal bankers or tellers make an average of $32,620 per year, according to the BLS. (wgu.edu)
- The profession is expected to grow 7% by 2028, a bit faster than the national average. (wgu.edu)
- The average salary for financial advisors in 2021 is around $60,000 per year, with the top 10% of the profession making more than $111,000 per year. (wgu.edu)
- UpCounsel accepts only the top 5 percent of lawyers on its site. (upcounsel.com)
- This field is expected to grow about 7% by 2028, a bit faster than the national average for job growth. (wgu.edu)
External Links
How To
How does Lean Manufacturing work?
Lean Manufacturing techniques are used to reduce waste while increasing efficiency by using structured methods. They were developed in Japan by Toyota Motor Corporation (in the 1980s). It was designed to produce high-quality products at lower prices while maintaining their quality. Lean manufacturing emphasizes removing unnecessary steps from the production process. It is composed of five fundamental elements: continuous improvement; pull systems, continuous improvements, just-in–time, kaizen, continuous change, and 5S. It is a system that produces only the product the customer requests without additional work. Continuous improvement is the continuous improvement of existing processes. Just-in–time refers when components or materials are delivered immediately to their intended destination. Kaizen means continuous improvement. Kaizen involves making small changes and improving continuously. The 5S acronym stands for sort in order, shine standardize and maintain. These five elements can be combined to achieve the best possible results.
The Lean Production System
Six key concepts form the foundation of the lean production system:
-
Flow - The focus is on moving information and material as close as possible to customers.
-
Value stream mapping - break down each stage of a process into discrete tasks and create a flowchart of the entire process;
-
Five S's - Sort, Set In Order, Shine, Standardize, and Sustain;
-
Kanban - use visual signals such as colored tape, stickers, or other visual cues to keep track of inventory;
-
Theory of constraints: identify bottlenecks in your process and eliminate them using lean tools, such as kanban board.
-
Just-in-time - deliver components and materials directly to the point of use;
-
Continuous improvement - Make incremental improvements rather than overhauling the entire process.