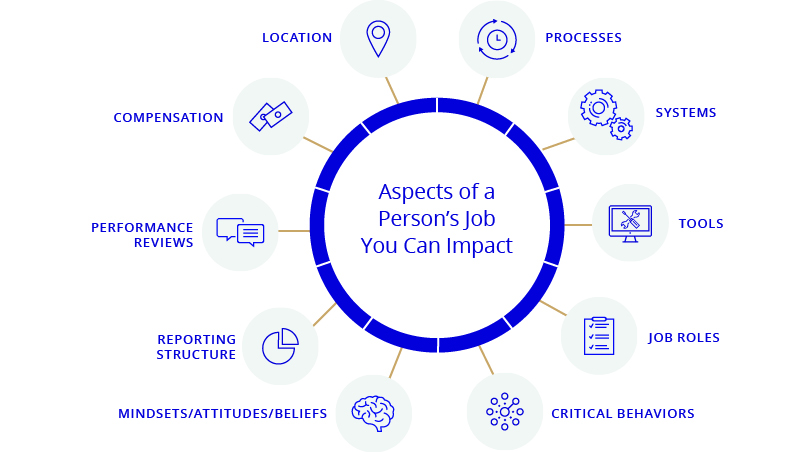
This approach is best suited for small, tight-knit projects. It is important that the project team coordinates early to address site-related issues. Owners must communicate clearly with their contractor and architect. In addition, they must trust and be clear about their expectations. If an owner is unsure, he can consult a project manager to explain the process.
IPD
IPD projects are a way to foster trust and cooperation among members of the team in order achieve common goals. It helps project participants define their project goals, risks and responsibilities. It promotes ownership of project tasks and equality among team members. It reduces rework by keeping project participants updated on progress.
The project owner creates an IPD team that includes key participants. To encourage teamwork, incentives are tied to milestones and goals of the project. The compensation of the participants is also tied to their performance. This aligns their financial interest, making the project costs predictable as well as affordable.
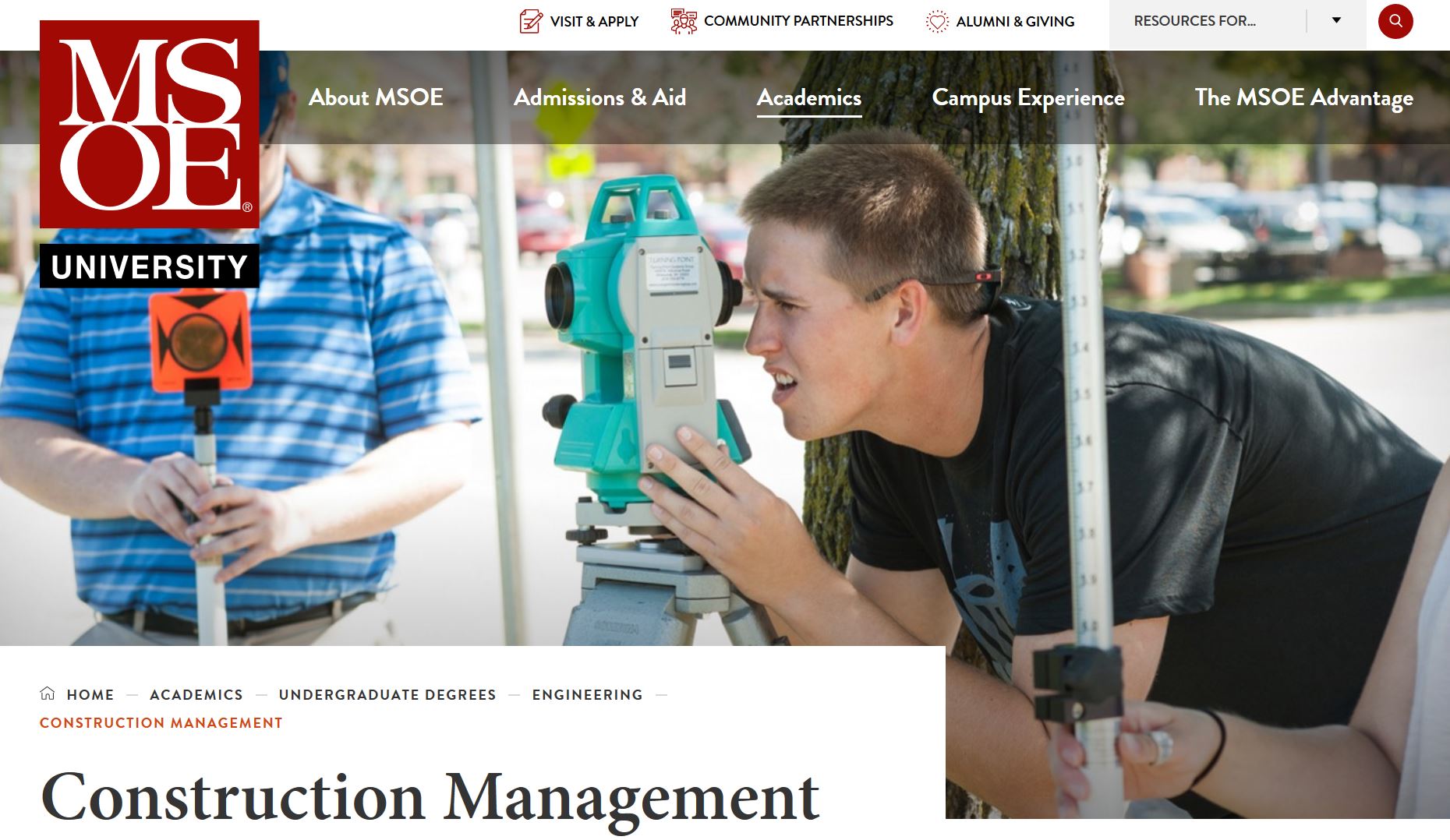
Design-Build
For many construction projects, the Design-Build project delivery option is a great choice. It allows the owner to have early involvement in the project planning and design phase. This early collaboration helps to eliminate potential conflicts between the owner and the contractor and results in lower construction costs and a faster project schedule. Additionally, a design-build contractor eliminates the need for an in-house project manager, which allows the owner to focus on the design aspects of the project.
The scope of work of a Design-Build project should be clearly defined in the contract documents. The contract documents should clearly define the scope of work for a Design-Build project. The contract should also outline the frequency of design submittals and the processes for review of these submissions.
Construction manager at risk
The construction manager at-risk (CMA at risk) delivery method is unique in that design as well as construction are separately contracted. This method selects the construction manager based not only on the lowest total cost of construction. The CM at risk is responsible to deliver the project according to the owner's specifications, within a maximum price guarantee. The construction manager serves as both a consultant to project owners during the development phase, and as a general contractor during construction.
This approach reduces risk for everyone. This type of project delivery method is not appropriate for all projects. The construction manager at risk, unlike Design-Build and Bid -Build is not an architect nor contractor. The construction manager must have high visibility to all project stakeholders. In addition, the project manager must stay under the guaranteed maximum price to avoid payment delays.
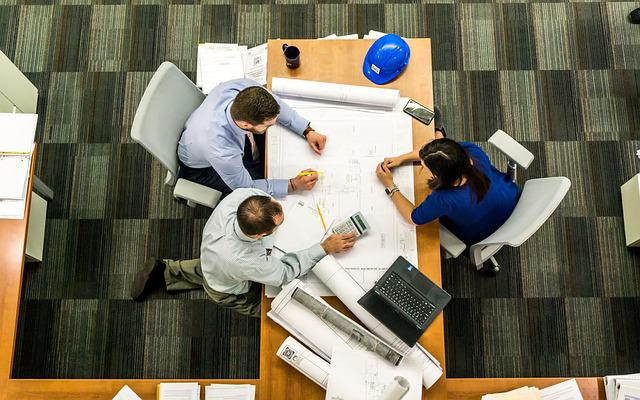
Integrated project delivery
All project stakeholders are involved in an integrated project delivery (IDP), from design to management. This approach allows all stakeholders to view the project holistically, which is a benefit to everyone. It also eliminates any waiting periods between construction phases which can lead to increased productivity. Additionally, key stakeholders can benefit from the involvement of their knowledge early on in the project. This will help to improve decision-making. This method also makes use of the most recent technological possibilities.
A project delivery approach that integrates all aspects of the construction process can be a great way for companies to deal with the problems. If a construction team fails to finish a project on schedule, they can use the Deming Cycle template to pinpoint the cause and take the appropriate actions. Additionally, the IPD process allows stakeholders to collaborate and work together towards a common goal.
FAQ
How does a manager motivate their employees?
Motivation is the desire for success.
Doing something that is enjoyable can help you get motivated.
Or you can get motivated by seeing yourself making a contribution to the success of the organization.
For example, if you want to become a doctor, you'll probably find it more motivating to see patients than to study medicine books all day.
Another type of motivation comes from within.
Perhaps you have a strong sense to give back, for example.
You might even enjoy the work.
If you don't feel motivated, ask yourself why.
Then, consider ways you could improve your motivation.
How does Six Sigma function?
Six Sigma employs statistical analysis to identify problems, measure them and analyze root causes. Six Sigma also uses experience to correct problems.
The first step is identifying the problem.
The next step is to collect data and analyze it in order to identify trends or patterns.
Next, corrective steps are taken to fix the problem.
The data are then reanalyzed to see if the problem is solved.
This cycle will continue until the problem is solved.
What is Six Sigma and how can it help you?
It's a method for quality improvement that focuses on customer service as well as continuous learning. It is a method that eliminates defects using statistical techniques.
Motorola developed Six Sigma in 1986 to help improve its manufacturing processes.
This idea quickly spread throughout the industry. Today, many organizations use six sigma methods for product design, production and delivery.
Which kind of people use Six Sigma
People who have worked with statistics and operations research will usually be familiar with the concepts behind six sigma. However, anyone involved in any aspect of business can benefit from using it.
It is a commitment-intensive task that requires strong leadership skills.
Statistics
- Our program is 100% engineered for your success. (online.uc.edu)
- UpCounsel accepts only the top 5 percent of lawyers on its site. (upcounsel.com)
- This field is expected to grow about 7% by 2028, a bit faster than the national average for job growth. (wgu.edu)
- Hire the top business lawyers and save up to 60% on legal fees (upcounsel.com)
- The BLS says that financial services jobs like banking are expected to grow 4% by 2030, about as fast as the national average. (wgu.edu)
External Links
How To
How is Lean Manufacturing done?
Lean Manufacturing techniques are used to reduce waste while increasing efficiency by using structured methods. They were created by Toyota Motor Corporation in Japan in the 1980s. The aim was to produce better quality products at lower costs. Lean manufacturing eliminates unnecessary steps and activities from a production process. It includes five main elements: pull systems (continuous improvement), continuous improvement (just-in-time), kaizen (5S), and continuous change (continuous changes). Pull systems allow customers to get exactly what they want without having to do extra work. Continuous improvement involves constantly improving upon existing processes. Just-in-time is when components and other materials are delivered at their destination in a timely manner. Kaizen means continuous improvement. Kaizen involves making small changes and improving continuously. Last but not least, 5S is for sort. These five elements work together to produce the best results.
The Lean Production System
The lean production system is based on six key concepts:
-
Flow - The focus is on moving information and material as close as possible to customers.
-
Value stream mapping - break down each stage of a process into discrete tasks and create a flowchart of the entire process;
-
Five S's: Sort, Shine Standardize, Sustain, Set In Order, Shine and Shine
-
Kanban: Use visual signals such stickers, colored tape, or any other visual cues, to keep track your inventory.
-
Theory of constraints: Identify bottlenecks and use lean tools such as kanban boards to eliminate them.
-
Just-in Time - Send components and material directly to the point-of-use;
-
Continuous improvement - Make incremental improvements rather than overhauling the entire process.