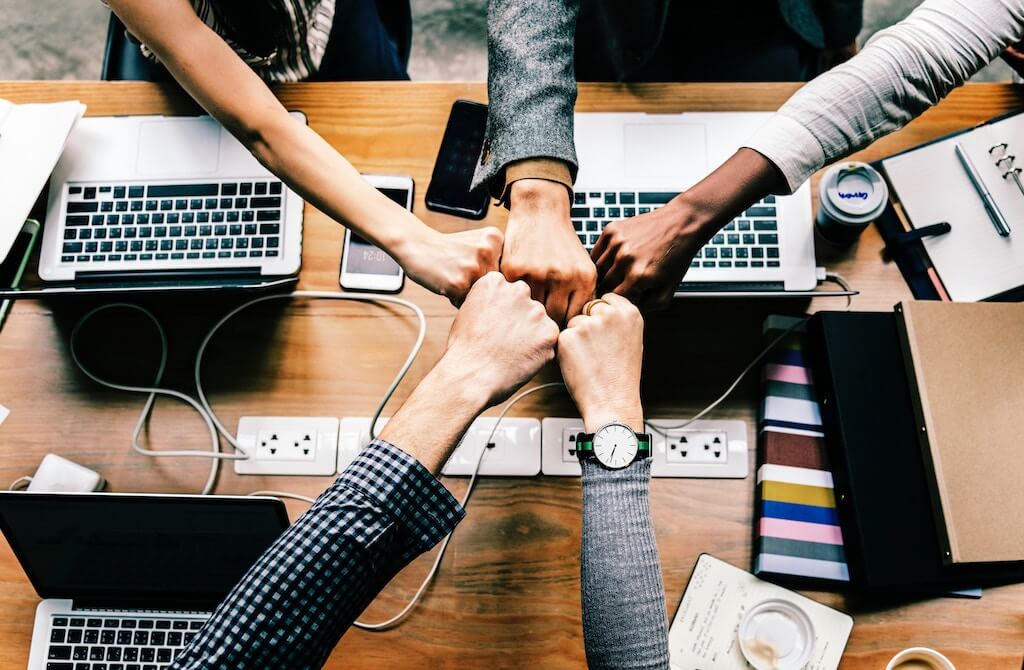
The Associate in Risk Management (ARM) program helps students learn how to master the rapidly evolving world of risk management. Graduates can manage all aspects of risk within their company confidently. The program will teach them about risk management, including financial, operational and strategic. It also gives them a global perspective. This program is technology-driven.
ARM designation
An ARM designation is a professional designation in risk management. This designation requires that a candidate demonstrate competence in risk assessment and hazard identification as well as risk response. The ARM designation is required for advancement to the Fellow Designation of RIMS, a non-profit organization that represents risk management professionals around the globe.
The ARM program prepares students for rapid technological changes in risk management. This education will prepare graduates to manage all kinds of risk in their workplaces. They will be able to manage financial, operational, and strategic risks. Students are also provided with a global perspective in risk management.
Courses
Associate in Risk Management (ARM), courses aim to teach students the rapidly changing field. The program provides students with the skills necessary to confidently handle all aspects of risk within an organization. Students learn to manage financial, operational, hazard and strategic risks. Students also learn about global risk management. Students will also benefit from a technology-driven view that will enable them to be successful in a career of risk management.
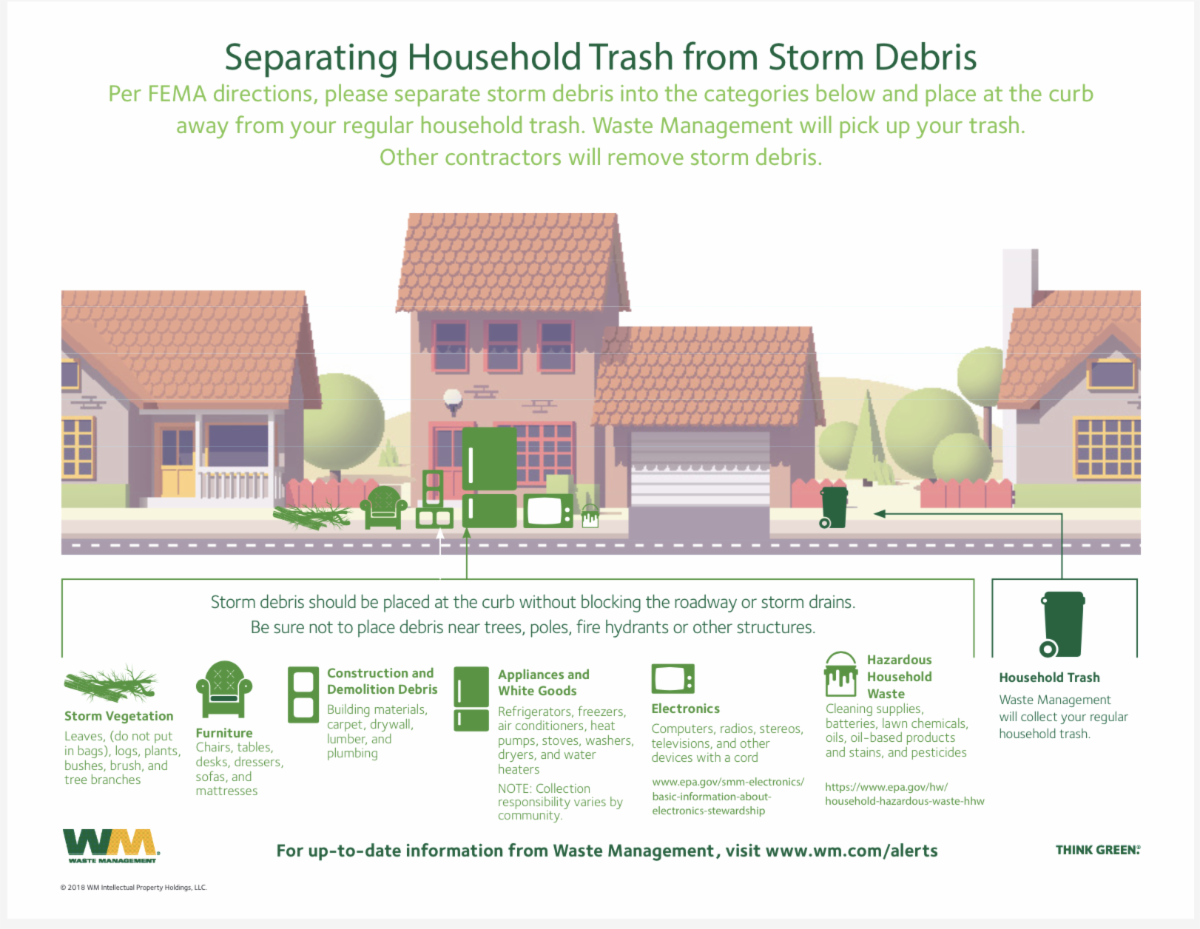
The courses offered at RISK management education institutions are varied. Some are intended for risk professionals and others for business people. Advanced courses concentrate on strategic risk management.
Exam
The Associate in Risk Management exam is a professional certification that allows you to be a risk manager. This exam includes both quantitative and qualitative methods in risk management. It also considers both opportunities and risks. This exam helps you to be more aware of risks and make informed decisions. It also helps to learn about risk quadrants as well as their importance.
For this certification students need to take three core courses along with a risk management ethic exam. This exam is composed of around 15 to 40 multiple choice questions. It is graded on an pass-fail basis. This exam is not for the weak of heart. Keir Educational Resources has study materials that can assist you in getting the Associate degree in risk management.
Pay range
ZipRecruiter reports that the average salary range for associates in risk management is between $53,500 and $79,500. The highest paid associates can earn as much $90,000. The actual range of pay can vary from $90,000 to $25,000 depending upon your location, employer and years of experience.
The salary range of associates in risk management will vary depending on where you work and how large your organization is. Higher salaries will be paid by larger companies located closer to the city. You will need a relevant degree from a university, solid knowledge about risk management policies and the ability manage and lead projects.
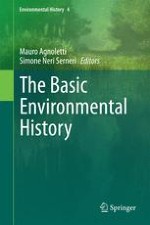
Free course for ARM candidates
The Institutes offers a free course to anyone who wants to become an Associate in Risk Management (ARM). The course will prepare you for the ARM exam. The course is offered at no cost and contains an online module entitled Ethical Guidelines For Insurance Professionals. The online course is free and candidates can receive up to 50 credit towards certification.
The Insurance Institute of America awards the Associate in Risk Management (ARM), a professional designation. It focuses on the science and principles of risk management, and involves methods for avoiding, minimizing, and managing risks. These courses are self-study and candidates must complete them before they can take the exam.
FAQ
What is the main difference between Six Sigma Six Sigma TQM and Six Sigma Six Sigma?
The major difference between the two tools for quality management is that six Sigma focuses on eliminating defect while total quality control (TQM), on improving processes and decreasing costs.
Six Sigma is a methodology for continuous improvement. It emphasizes the elimination of defects by using statistical methods such as control charts, p-charts, and Pareto analysis.
This method aims to reduce variation in product production. This is done by identifying root causes and rectifying them.
Total quality management involves measuring and monitoring all aspects of the organization. This includes training employees to improve their performance.
It is commonly used as a strategy for increasing productivity.
What is a fundamental management tool for decision-making?
A decision matrix is a simple but powerful tool for helping managers make decisions. It helps them to think strategically about all options.
A decision matrix is a way of representing alternatives as rows and columns. This allows you to easily see how each choice affects others.
The boxes on the left hand side of this matrix represent four possible choices. Each box represents an option. The top row depicts the current status quo, while the bottom row represents what would happen if no action was taken.
The effect of Option 1 can be seen in the middle column. This would result in an increase of sales of $2 million to $3million.
The following columns illustrate the impact of Options 2 and 3. These positive changes can increase sales by $1 million or $500,000. But, they also have some negative consequences. Option 2, for example, increases the cost by $100 000 while Option 3 decreases profits by $200 000.
Finally, the last column shows the results of choosing Option 4. This would result in a reduction of sales of $1 million.
A decision matrix has the advantage that you don’t have to remember where numbers belong. The best thing about a decision matrix is that you can simply look at the cells, and immediately know whether one option is better or not.
This is because the matrix has already taken care of the hard work for you. It's simply a matter of comparing the numbers in the relevant cells.
Here is an example how you might use the decision matrix in your company.
It is up to you to decide whether to spend more money on advertising. By doing so, you can increase your revenue by $5 000 per month. However, this will mean that you'll have additional expenses of $10,000.
By looking at the cell just below "Advertising", the net result can be calculated as $15 thousand. Advertising is worth more than its cost.
What can a manager do to improve his/her management skillset?
It is important to have good management skills.
Managers should monitor the performance and progress of their subordinates.
It is important to take immediate action if your subordinate doesn't perform as expected.
It is important to be able identify areas that need improvement and what can be done to improve them.
How do you define Six Sigma?
Six Sigma will most likely be familiar to people who have worked in statistics and operations research. Anyone involved in business can benefit.
It requires high levels of commitment and leadership skills to be successful.
How do you effectively manage employees?
The key to effective management of employees is ensuring their happiness and productivity.
It is important to set clear expectations about their behavior and keep track of their performance.
Managers need to establish clear goals for their team and for themselves.
They should communicate clearly with employees. They should also ensure that they both reward high performers and discipline those who are not performing to their standards.
They must also keep track of the activities of their team. These include:
-
What was achieved?
-
How much work did you put in?
-
Who did it and why?
-
It was done!
-
Why was it done?
This information can be used for monitoring performance and evaluating results.
What are the 4 main functions of management?
Management is responsible for planning, organizing, directing, and controlling people and resources. It includes creating policies and procedures, as well setting goals.
Management aids an organization in reaching its goals by providing direction and coordination, control, leadership motivation, supervision, training, evaluation, and leadership.
These are the four major functions of management:
Planning - Planning is about determining what must be done.
Organizing - Organizing involves deciding how things should be done.
Direction - This is the art of getting people to follow your instructions.
Controlling - Controlling means ensuring that people carry out tasks according to plan.
What does it mean to say "project management"
We mean managing the activities involved in carrying out a project.
These include planning the scope and identifying the needs, creating the budget, organizing the team, scheduling the work and monitoring progress. Finally, we close down the project.
Statistics
- The BLS says that financial services jobs like banking are expected to grow 4% by 2030, about as fast as the national average. (wgu.edu)
- 100% of the courses are offered online, and no campus visits are required — a big time-saver for you. (online.uc.edu)
- This field is expected to grow about 7% by 2028, a bit faster than the national average for job growth. (wgu.edu)
- The profession is expected to grow 7% by 2028, a bit faster than the national average. (wgu.edu)
- The average salary for financial advisors in 2021 is around $60,000 per year, with the top 10% of the profession making more than $111,000 per year. (wgu.edu)
External Links
How To
What is Lean Manufacturing?
Lean Manufacturing is a method to reduce waste and increase efficiency using structured methods. They were developed in Japan by Toyota Motor Corporation (in the 1980s). The goal was to produce quality products at lower cost. Lean manufacturing is about eliminating redundant steps and activities from the manufacturing process. It has five components: continuous improvement and pull systems; just-in time; continuous change; and kaizen (continuous innovation). It is a system that produces only the product the customer requests without additional work. Continuous improvement is the continuous improvement of existing processes. Just-intime refers the time components and materials arrive at the exact place where they are needed. Kaizen refers to continuous improvement. It is achieved through small changes that are made continuously. Last but not least, 5S is for sort. These five elements are used together to ensure the best possible results.
Lean Production System
Six key concepts are the basis of lean production:
-
Flow - The focus is on moving information and material as close as possible to customers.
-
Value stream mapping - Break down each stage in a process into distinct tasks and create an overview of the whole process.
-
Five S's: Sort, Shine Standardize, Sustain, Set In Order, Shine and Shine
-
Kanban - visual cues such as stickers or colored tape can be used to track inventory.
-
Theory of constraints - identify bottlenecks in the process and eliminate them using lean tools like kanban boards;
-
Just-in time - Get components and materials delivered right at the point of usage;
-
Continuous improvement is making incremental improvements to your process, rather than trying to overhaul it all at once.