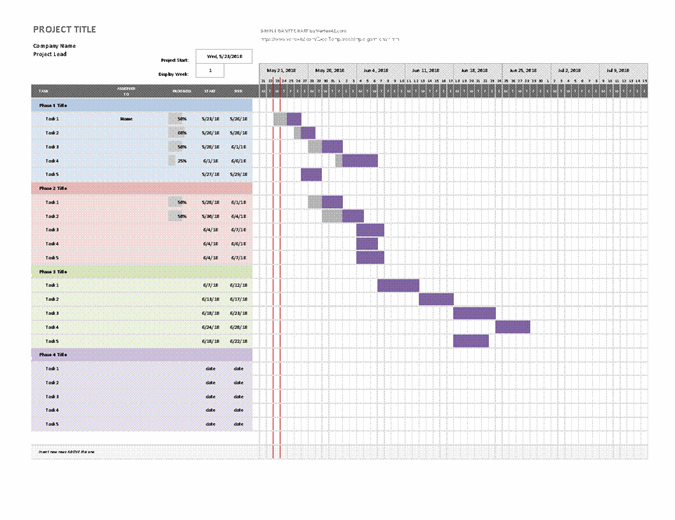
What is Credit Risk and how can it be managed? Credit risk is the risk that a lender takes on when extending credit to a borrower. This risk is usually caused by the borrower's failure to pay the loan terms. Credit risk is not only a loss of principal or interest but can also cause cash flow disruptions, and increase collection costs. Lenders should be aware that the risk could be total or partial. When determining the right lending strategy, a lender must be aware of the various credit risks that may exist.
Measuring
Financial institutions should be very concerned about measuring credit risk. This is because it is essential to understand the credit behavior and avoid future losses. Credit risk management Information Systems (CRMIS), calculate the likelihood that a customer might default on their loan obligations. This information is valuable for credit lenders, solidarity organizations, financial institutions and all other entities involved in credit lending. Here are some tips on how to measure credit risk.
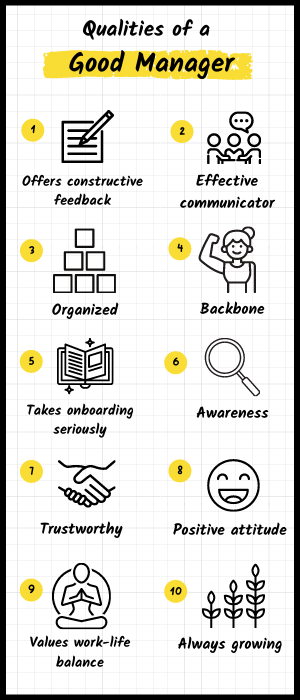
Analyse
Analyzing credit risk is a process that uses financial information to determine the probability of a borrower defaulting on a loan. It uses both information within the company and external data to predict the likely consequences of default. It is essential to be able to accurately forecast credit risk and minimize adverse consequences. Credit risk can be quantified and has an immediate impact on financial institution activities. Here are some basics about credit risk analysis.
Pricing
A lot of attention has been paid to developing sophisticated models for pricing credit risks due to recent growth in structured products. These models have been sparked by regulatory concerns and empirical data about default rates. This article reviews the progress in credit risk modeling over three decades. It discusses the statistical properties of credit spreads across time as well as the quantitative models for assessing creditworthiness. The article concludes with policy implications for credit pricing.
Sector exposure
Financial professionals often mistakenly believe that credit risk and sector exposure are interchangeable. In fact, the two terms are different but often referred to as the same. They are also closely related. A single factor can actually affect both. A bank's sector exposure may be a risk factor, but credit risk can determine a firm’s creditworthiness.
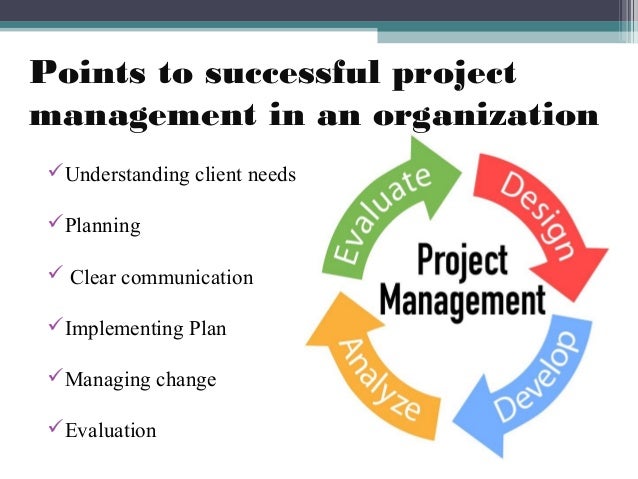
Diversification
Diversifying investments across assets and types can reduce credit risk. Diversifying the portfolio will reduce your risk of short-term losses, and increase your chances of achieving upside. Diversifying your assets will reduce specific risks, such as market volatility, which can be caused by wars, political conflict, and interest rate changes. You can also use it to help you reach your long-term financial goals by minimizing risk and maximising your returns.
FAQ
What are the main four functions of management
Management is responsible in planning, organizing and directing people and resources. It includes creating policies and procedures, as well setting goals.
Management helps an organization achieve its objectives by providing direction, coordination, control, leadership, motivation, supervision, training, and evaluation.
The four main functions of management are:
Planning - Planning is about determining what must be done.
Organizing – Organizing means deciding how to organize things.
Directing – This means to get people to follow directions.
Controlling - Controlling means ensuring that people carry out tasks according to plan.
What are the key management skills?
Management skills are essential for any business owner, whether they're running a small local store or an international corporation. These include the ability and willingness to manage people, finances as well resources, time and space.
These skills are necessary for setting goals and objectives as well as planning strategies, leading groups, motivating employees and solving problems.
As you can see, there's no end to the list of managerial duties!
What is Six Sigma, exactly?
It is a way to improve quality that places emphasis on customer service and continuous learning. This is an approach to quality improvement that uses statistical techniques to eliminate defects.
Motorola invented Six Sigma in 1986 as part its efforts to improve manufacturing.
The idea spread quickly in the industry. Today many organizations use six-sigma techniques to improve product design.
What is the difference in leadership and management?
Leadership is all about influencing others. Management is about controlling others.
Leaders inspire followers, while managers direct workers.
A leader motivates people and keeps them on task.
A leader develops people; a manager manages people.
Why is project management important for companies?
To ensure projects run smoothly and meet deadlines, project management techniques are employed.
This is due to the fact that most businesses rely heavily upon project work in order to produce goods, and services.
Companies need to manage these projects efficiently and effectively.
Companies that do not manage their projects effectively risk losing time, money, or reputation.
What is the difference between TQM and Six Sigma?
The key difference between the two quality management tools is that while six-sigma focuses its efforts on eliminating defects, total quality management (TQM), focuses more on improving processes and reducing cost.
Six Sigma can be described as a strategy for continuous improvement. It emphasizes the elimination or minimization of defects through statistical methods such control charts and p charts.
This method attempts to reduce variations in product output. This is done by identifying and correcting the root causes of problems.
Total quality management refers to the monitoring and measurement of all aspects in an organization. This includes training employees to improve their performance.
It is often used as a strategy to increase productivity.
Statistics
- Your choice in Step 5 may very likely be the same or similar to the alternative you placed at the top of your list at the end of Step 4. (umassd.edu)
- Hire the top business lawyers and save up to 60% on legal fees (upcounsel.com)
- The profession is expected to grow 7% by 2028, a bit faster than the national average. (wgu.edu)
- UpCounsel accepts only the top 5 percent of lawyers on its site. (upcounsel.com)
- 100% of the courses are offered online, and no campus visits are required — a big time-saver for you. (online.uc.edu)
External Links
How To
How does Lean Manufacturing work?
Lean Manufacturing processes are used to reduce waste and improve efficiency through structured methods. They were developed in Japan by Toyota Motor Corporation (in the 1980s). The primary goal was to make products with lower costs and maintain high quality. Lean manufacturing is about eliminating redundant steps and activities from the manufacturing process. It has five components: continuous improvement and pull systems; just-in time; continuous change; and kaizen (continuous innovation). It is a system that produces only the product the customer requests without additional work. Continuous improvement means continuously improving on existing processes. Just-in-time refers to when components and materials are delivered directly to the point where they are needed. Kaizen means continuous improvement, which is achieved by implementing small changes continuously. Last but not least, 5S is for sort. These five elements are combined to give you the best possible results.
Lean Production System
Six key concepts make up the lean manufacturing system.
-
Flow: The goal is to move material and information as close as possible from customers.
-
Value stream mapping- This allows you to break down each step of a process and create a flowchart detailing the entire process.
-
Five S's – Sort, Put In Order Shine, Standardize and Sustain
-
Kanban – visual signals like colored tape, stickers or other visual cues are used to keep track inventory.
-
Theory of constraints: identify bottlenecks in your process and eliminate them using lean tools, such as kanban board.
-
Just-intime - Order components and materials at your location right on the spot.
-
Continuous improvement - Make incremental improvements rather than overhauling the entire process.